Im Vergleich zu anderen Oxidkeramikmembranen ( Aluminiumoxid, Titanoxid, Zirkonoxid usw.) weist Siliziumkarbidmembranrohre eine höhere Hydrophilie, Durchlässigkeit, Verschmutzungsbeständigkeit und chemische Stabilität auf. Die Sintertemperatur der SIC-Keramikmembran hängt eng mit der Sintertechnologie zusammen. Zu den gängigen Sintertechnologien gehören Rekristallisationstechnologie, Keramikvorläuferumwandlungstechnologie und In-situ-Reaktionssintertechnologie.
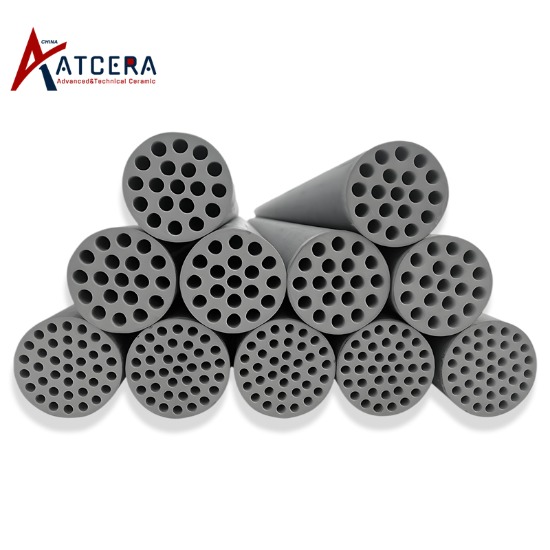
Rekristallisationssintertechnologie
Die Rekristallisationssintertechnologie bezieht sich auf die Realisierung der Wiedervereinigung von SiC-Partikeln gemäß dem Verdampfungs-Kondensations-Gasphasenmigrationsmechanismus unter Hochtemperatursinterung. Dieser Prozess beinhaltet keine zu großen chemischen Reaktionen, die Porengröße wird stark von der Größe des Rohmaterialpulvers beeinflusst, die erhaltene Siliziumkarbidmembranporenstruktur ist gleichmäßig und der Zickzackfaktor ist niedrig. Da Siliziumkarbid bei hohen Temperaturen, hohem Druck und einem breiten pH-Bereich eine gute Stabilität aufweist, werden Sinterzusätze und eine Bipeak-Verteilung von Siliziumkarbidpulver im Allgemeinen verwendet, um die Sintertemperatur während der Rekristallisation zu senken. Das durch Rekristallisationssintertechnologie hergestellte Siliziumkarbidmembranrohr weist eine hohe chemische Stabilität auf, aber seine Sintertemperatur ist hoch (> 1800 °C), der Energieverbrauch ist hoch und während des Sinterprozesses ist der Schutz vor inerter Atmosphäre erforderlich, und die Ausrüstung ist äußerst anspruchsvoll. Um außerdem den möglichen Restkohlenstoff in den Poren zu entfernen, muss nach Abschluss des Sinterns die Oberflächenoxidation in einer Luftatmosphäre unter 800 °C durchgeführt werden, was den Herstellungsprozess kompliziert macht.
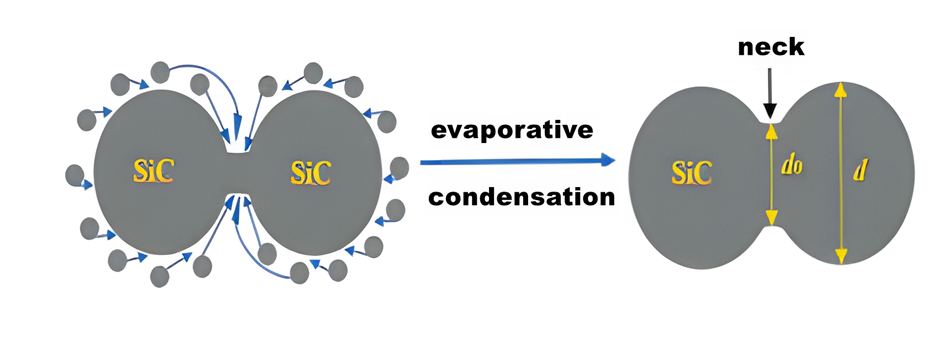
SiC-Hochtemperatur-Rekristallisationsdiagramm
Technologie zur Umwandlung keramischer Vorläufer
Bei der Keramikvorläufer-Konversionstechnologie wird siliziumhaltiges organisches Polymer (wie Silikonharz, Polycarbosilan usw.) in einer inerten Atmosphäre und in einem bestimmten Temperaturbereich (1100–1600 °C) gespalten, um eine Bindungsphase zwischen Siliziumkarbidaggregaten zu bilden und so eine Siliziumkarbid-Keramikmembran mit einer bestimmten mechanischen Festigkeit herzustellen. Die Keramikvorläufer-Konversionstechnologie stellt nur geringe Anforderungen an die Sintertemperatur, was den Energieverbrauch senkt. Allerdings besteht der Rohstoff aus hochpolymerem Material und der Sinterprozess erfordert eine anaerobe Atmosphäre, was die Nachteile hoher Kosten und eines komplexen Prozesses mit sich bringt, der für die industrielle Produktion nicht förderlich ist. Um das Anwendungspotenzial der Keramikvorläufer-Konversionstechnologie für die Membranproduktion weiterzuentwickeln und zu optimieren, ist es notwendig, sich auf Kostensenkung und Mikrostrukturregulierung (Porengröße, Porosität und Membrandicke) zu konzentrieren.
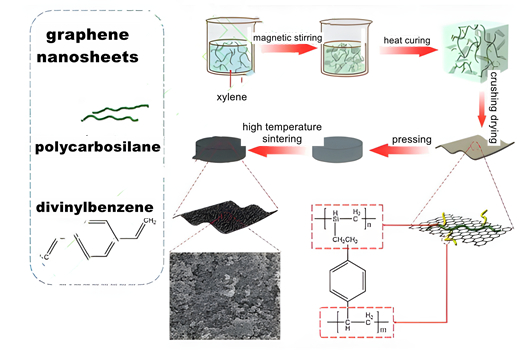
Herstellung einer Siliziumkarbid-Keramikmembran durch Keramikvorläufer-Konversionstechnologie
In-Situ-Reaktionssintertechnologie
Bei der In-situ-Reaktionssintertechnologie werden Siliziumkarbid-Aggregatpartikeln unter Luftatmosphäre Sinteradditive zugesetzt, sodass Siliziumoxid entsteht, das viel niedriger ist als die Sintertemperatur einer reinen Siliziumkarbid-Keramikmembran (1350–1550 °C). Anschließend erfolgt die In-situ-Reaktion mit dem Sintermittel, um eine Halsverbindung zu bilden. Übliche Sinteradditive sind hauptsächlich Metalloxide wie Aluminiumoxid, Yttriumoxid und Zirkonoxid. Im Reaktionsprozess werden Mullit, Cordierit und andere Mehrkomponentenoxide zur Bindungsphase der Halsverbindung zwischen den Partikeln. Die Zugabe dieser Sinteradditive fördert die Änderung der Korngrenzen und der Oberflächenenergie des SIC-Aggregats, wodurch die Massendiffusionsrate im Sinterprozess beschleunigt und die Sinterkosten gesenkt werden. Die In-situ-Reaktivsintertechnologie kann die Sintertemperatur von SIC wirksam senken, der Membranherstellungsprozess muss jedoch noch verkürzt werden.
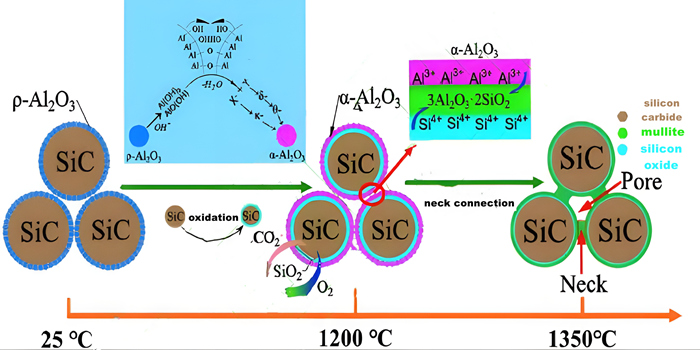
Schematische Darstellung des Sinterprozesses von mullitgebundener poröser Siliziumkarbidkeramik, hergestellt durch reaktives In-situ-Sinterverfahren
Um das industrielle Anwendungspotenzial von Siliziumkarbid-Membranrohren weiter zu verbessern, kann man dies unter den Gesichtspunkten der Kostensenkung und Leistungssteigerung betrachten. Um die Kosten zu senken, kann man beispielsweise kostengünstige Polymervorläufer verwenden, um Siliziumkarbid-Membranen mit kleiner Porengröße zur Gastrennung herzustellen. Außerdem kann man die Kombination von Sinteradditiven optimieren, die Sintertemperatur senken und den Anwendungsbereich der Co-Sintertechnologie weiter erweitern.
Angesichts der weltweiten Sorge um den Umweltschutz ist die Nachfrage nach Hochleistungsfiltrations- und Trenntechnologie immer dringlicher geworden, was wertvolle Möglichkeiten für die Entwicklung und Anwendung von Siliziumkarbid-Membranrohren bietet. Auch in Zukunft werden noch viele Ressourcen benötigt, um die Probleme der unausgereiften Produktions- und Vorbereitungstechnologie für Keramikmembranen zu lösen, damit die Trenntechnologie für Siliziumkarbid-Keramikmembranen mehr praktische Anwendung finden kann.