Wissenschaftler haben herausgefunden, dass Mikrostruktur und Sauerstoffverunreinigungsgehalt die beiden wichtigsten Faktoren sind, die die Wärmeleitfähigkeit von AlN-Keramik beeinflussen. Um die Wärmeleitfähigkeit von AlN-Keramik zu verbessern, muss daher der Vorbereitung der Keramikpulver-Rohstoffe und dem Sinterprozess mehr Aufmerksamkeit geschenkt werden. Kontinuierliche experimentelle Untersuchungen zeigen, dass die Verfeinerung des ursprünglichen Aluminiumnitridpulvers und die Zugabe geeigneter Niedertemperatur-Sinterzusätze erforderlich sind effektive Lösungen.
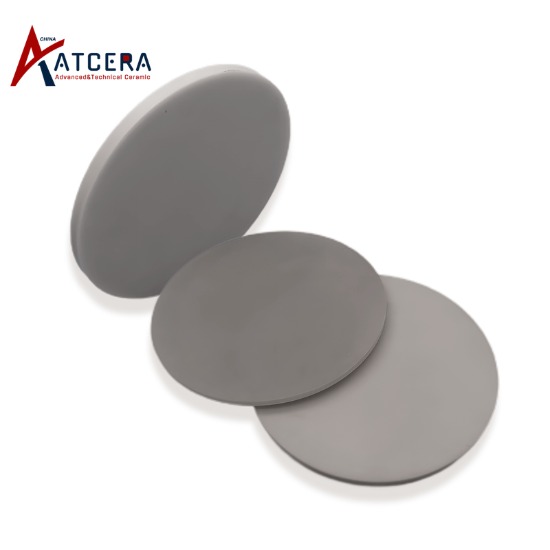
Die Auswahl der Pulverrohstoffe
Aluminiumnitridpulver ist die Voraussetzung und der Schlüssel zur Herstellung von Aluminiumnitrid-Keramikmaterialien mit hervorragenden Eigenschaften. Die treibende Kraft des Aluminiumnitrid-Sinterprozesses ist die Oberflächenenergie, und feine AlN-Pulverpartikel können die Sinteraktivität verbessern, die Sinterkraft erhöhen und den Sinterprozess beschleunigen. Es wird bestätigt, dass sich die Sinterrate der Keramik um das 147-fache erhöht, wenn die anfängliche Partikelgröße des ursprünglichen Aluminiumnitridpulvers 20-mal kleiner ist.
Gleichzeitig sollte die Partikelgröße des ursprünglichen Pulvers fein und gleichmäßig sein, um eine sekundäre Rekristallisation zu verhindern. Wenn das Partikel eine kleine Anzahl großer Partikel enthält, kann es leicht zu abnormalem Kornwachstum kommen, was jedoch nicht der Fall ist fördert die Verdichtung und Sinterung; Wenn die Partikelverteilung nicht gleichmäßig ist, kann es während des Sinterprozesses leicht zu einem abnormalen Wachstum einzelner Kristalle kommen, das sich auf das Sintern auswirkt.
Darüber hinaus wird der Sintermechanismus von Aluminiumnitridkeramik manchmal durch die Größe des ursprünglichen Pulvers beeinflusst. Das mikrometergroße Aluminiumnitridpulver wird nach dem Volumendiffusionsmechanismus gesintert, während das nanoskalige Pulver nach dem Korngrenzendiffusions- oder Oberflächendiffusionsmechanismus gesintert wird.
Kuramot et al. zeigten, dass unter der Voraussetzung, dass keine Niedertemperatur-Sinteradditive hinzugefügt werden, Aluminiumnitrid selbst bei einer hohen Temperatur von 1900 °C kein dichtes Brennen erreichen kann, wenn die spezifische Oberfläche des Aluminiumnitridpulvers etwa 3 m 2 /g beträgt Die Partikelgröße betrug 80–100 nm, die spezifische Oberfläche betrug 40–50 m 2 /g und die Partikelgröße betrug etwa 0,11 μm. Das Aluminiumnitridpulver mit einer spezifischen Oberfläche von 16,6 m2/g kann grundsätzlich die theoretische Dichte erreichen, wenn es bei 1700 °C gesintert wird.
Hashimoto, Panchula und Ying bestätigten, dass durch Zugabe einer geeigneten Menge Nanometer-Aluminiumnitridpulver zum ursprünglichen Aluminiumnitridpulver ein kompaktes Sintern von Aluminiumnitridkeramik bei 1700 °C unter Normaldruck erreicht werden kann. Watari et al. Die Untersuchungen zeigen auch, dass die Sinterleistung von AL-Nitridkeramik direkt proportional zur Feinheit des Originalpulvers ist, d. h. je feiner das Originalpulver, desto besser die Sinterleistung.
Obwohl die Auswahl eines Pulvers mit feiner und gleichmäßiger Partikelgröße die Sintertemperatur von Aluminiumnitridkeramiken bis zu einem gewissen Grad senken kann, ist es schwierig, ein feines und gleichmäßiges Aluminiumnitrid-Pulversystem herzustellen, und zwar meist nicht nur durch nasschemische Verfahren in Kombination mit der carbothermischen Reduktionsmethode Da der Sinterprozess komplex und der Energieverbrauch hoch ist, eignet er sich nicht für die Förderung und Anwendung in großem Maßstab. Durch die Zugabe geeigneter Sinteradditive kann die Sintertemperatur von AlN-Keramiken deutlich gesenkt und einige Eigenschaften von AlN-Keramiken verbessert werden. Gegenwärtig wird diese Methode in großem Umfang angewendet und untersucht.
Die Auswahl von Sinteradditiven
Derzeit die beliebteste Methode zum Sintern von Aluminiumnitrid-Substrat ist die Zugabe geeigneter Sinteradditive und das Sintern unter Normaldruck. Diese Methode kann nicht nur den Energieverbrauch erheblich senken, sondern auch Hochleistungs-AlN-Keramik herstellen. Die Ergebnisse zeigen, dass die flüssige Phase im Sinterprozess von Al-Nitrid durch Zugabe einiger Sinterzusätze mit niedrigem Schmelzpunkt erzeugt werden kann und das dichte Sintern des Al-Nitrid-Embryos gefördert werden kann.
Darüber hinaus können einige Sinteradditive nicht nur eine flüssige Phase erzeugen, um das Sintern zu fördern, sondern auch mit Sauerstoffverunreinigungen im Aluminiumnitridgitter reagieren, um Sauerstoffverunreinigungen zu entfernen und das Gitter zu reinigen, wodurch die Wärmeleitfähigkeit von AlN-Keramik verbessert wird. Sinteradditive können jedoch nicht blind zugesetzt werden, die Zugabemenge sollte ebenfalls angemessen sein, da es sonst zu einer nachteiligen Wirkung kommen kann. Beispielsweise führt eine übermäßige Zugabe von Sinteradditiven zur Entstehung einer großen Anzahl zweiter Phasen, die die Wärmeleitfähigkeit von AlN deutlich verringern.
Hirano et al. erhielten verdichtete AlN-Keramik mit einer Wärmeleitfähigkeit von nur 114 W/m·K, indem AlN-Pulver ohne Zugabe von Sinterzusätzen 8 Stunden lang bei 1900 °C gehalten wurde, während die Wärmeleitfähigkeit durch Zugabe von 4 % Y2O3 unter den gleichen Bedingungen auf 218 W/m·K anstieg. Liu et al. untersuchten das Sintern von AlN-Keramik unter einer N2-Atmosphäre bei 1650 °C ohne Druck mit Dy 23 als Sintermittel und erhielten AlN-Keramik mit einer Wärmeleitfähigkeit von 156 W/m·k. Die Ergebnisse zeigten, dass Dy 23 Sauerstoffverunreinigungen in Aluminiumnitrid wirksam entfernen und die Wärmeleitfähigkeit von ALN-Keramik verbessern kann. Watari et al. LiYO 2-CaO hinzugefügt und bei 1600 °C gesintert, um AlN-Keramik mit einer Wärmeleitfähigkeit von mehr als 170 W/m·K zu erhalten. Zhou Heping und Qiao Liang erreichten das kompakte Sintern von Aluminiumnitridkeramiken bei einer niedrigen Sintertemperatur von 1650 °C durch Zugabe eines Verbundsintermittels CaF 2-y 2 O 3-Li 2 CO 3 zu Aluminiumnitrid, und die Wärmeleitfähigkeit war wie folgt hoch bis zu 177 W/m·K.