Mit der kontinuierlichen Weiterentwicklung der mikroelektronischen Verpackungstechnologie ist die Leistungsdichte elektronischer Komponenten erheblich gestiegen, was zu einem starken Anstieg der Wärmeerzeugung pro Volumeneinheit geführt hat, was zu strengeren Standards für die Leistung der neuen Generation von Leiterplatten geführt hat der Wärmeableitungseffizienz (Wärmeleitfähigkeit). Derzeit erforschen und entwickeln Forscher aktiv mehrere keramische Substratmaterialien mit hoher Wärmeleitfähigkeit, darunter Aluminiumnitrid (AlN), Siliziumkarbid (SiC) und Berylliumoxid (BeO). ). Allerdings sind BEOs aufgrund ihrer potenziellen Toxizität ökologisch begrenzt; Aufgrund seiner hohen Dielektrizitätskonstante gilt SiC nicht als ideales Substratmaterial. Im Gegensatz dazu ist AlN aufgrund seines ähnlichen Wärmeausdehnungskoeffizienten wie Silizium (Si) und seiner moderaten Dielektrizitätskonstanteneigenschaften zu einer beliebten Wahl für Substratmaterialien geworden.
Traditionell wurden Dickschichtaufschlämmungen hauptsächlich auf der Basis von Aluminiumoxidsubstraten (Al2O3) entwickelt. Die Komponenten dieser Aufschlämmungen neigen jedoch bei Kontakt mit AlN-Substraten zu chemischen Reaktionen und erzeugen Gas, was eine ernsthafte Bedrohung für die Stabilität und Leistung von Dickschichtschlämmen darstellt Filmschaltungen. Da der Wärmeausdehnungskoeffizient des AlN-Substrats außerdem niedriger ist als der des Al2O3-Substrats, führt die direkte Verwendung des für Al2O3 entwickelten Aufschlämmungs- und Sinterprozesses auf dem AlN-Substrat zu einer Fehlanpassung der Wärmeausdehnung, was zu Problemen führen wird. Daher ist es nicht ratsam, das für das Al2O3-Substrat anwendbare Materialsystem und den Produktionsprozess einfach auf das AlN-Substrat zu übertragen. Dieser Artikel konzentriert sich auf den Herstellungsprozess von Widerständen auf AlN-Substrat, erörtert den Herstellungsprozess eingehend und bewertet und analysiert die Leistung von Widerständen im Detail.
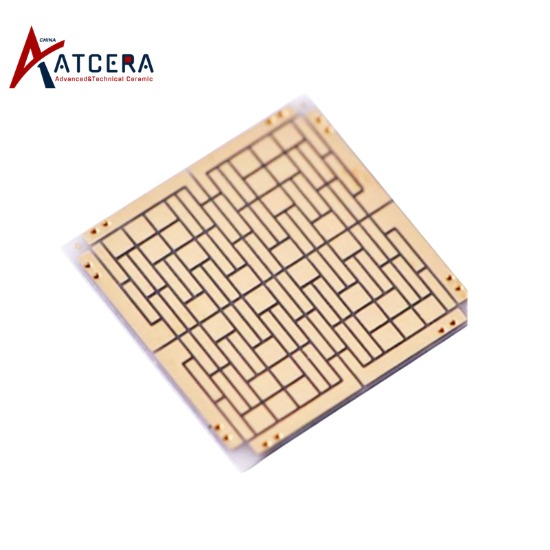
Widerstandsdesignnummer
Um die Beziehung zwischen dem Widerstandswert des AlN-Substrats und der Anzahl der Designquadrate zu bestimmen, wurde die Widerstandstestplatte entworfen (wie in Abbildung 4 dargestellt). Die Länge des Widerstands reicht von 500 bis 2000 μm und die Breite von 500 bis 2500 μm. Die Widerstände von vier Arten von quadratischen Widerständen wurden auf das AlN-Substrat gedruckt, und der Film wurde bei 850 °C gesintert, und die Widerstandswerte der Widerstände unterschiedlicher Designgrößen wurden gemessen.

Der Widerstandswert von drei Substraten gleicher Größe wird gemessen, die Designquadratzahl des Größenwiderstands wird berechnet, der Widerstandswert der drei Widerstände wird gemittelt und die Beziehung zwischen dem Widerstandswert und der Quadratzahl des Es bilden sich vier Arten von quadratischen Widerständen (wie in Abbildung 2 dargestellt).
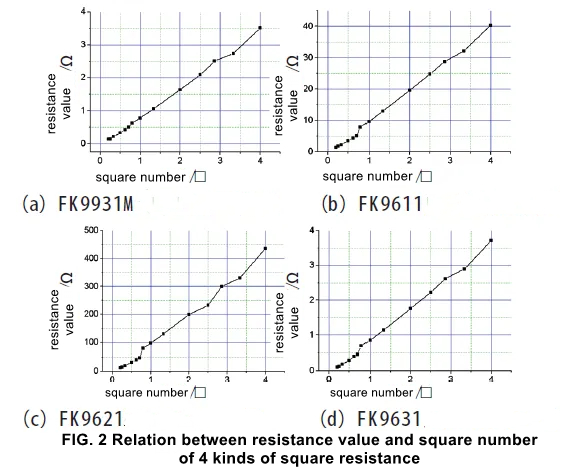
Wenn der Anfangswert des Widerstandsdrucks im Allgemeinen auf 80 % des Nennwerts ausgelegt ist, ist dies der Verbesserung des Einstellwerts und der Ausbeute am förderlichsten. Kombiniert mit dem Beziehungsdiagramm zwischen Widerstandswert und Quadratzahl wird das Auslegungsverhältnis der vier Quadratwiderstände berechnet (siehe Tabelle 1).
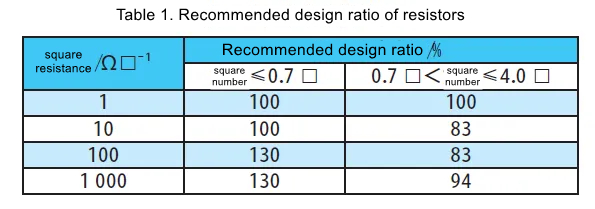
Widerstandswert-Anpassungsprozess
Bei der tatsächlichen Herstellung von Dickschichtwiderständen kann der Fehler zwischen dem Widerstandswert und dem Zielwert nur ±20 % erreichen, selbst wenn die Zusammensetzung der Aufschlämmung, das Druckverfahren, die Filmdicke, das Brennen und die Elektrodenanpassung streng kontrolliert werden. Um auf der Grundlage des hergestellten Dickschichtwiderstands den Widerstandswert mit der erforderlichen Präzision zu erhalten, kann der Wert nur angepasst werden. Im Hinblick auf die Verbesserung der Präzision des Ertrags- und Widerstandswerts ist die Wertanpassung eine wesentliche und wichtige Technologie.
Die Prozessparameter der Widerstandseinstellung auf AlN-Substrat sind wie folgt: Strom 14,5 A, Q-Frequenz 2500 Hz, Laserpunktabstand 150. Basierend auf der Analyse der Form der Schnittmarken nach der Einstellung, der Breite der Widerstandsschnittmarken der vier Der quadratische Widerstand ist größer als 30 μm und es gibt keinen Widerstand und keine Substratreste in den Schnittmarken, was den relevanten Anforderungen der Prüfdokumente entspricht.
Zusammenfassend lässt sich sagen, dass mit der rasanten Entwicklung der mikroelektronischen Verpackungstechnologie die Anforderungen an die Wärmeableitungseffizienz der Leiterplatte steigen, was die Forschung und Entwicklung von Keramiksubstratmaterialien mit hoher Wärmeleitfähigkeit fördert. Unter ihnen sticht Aluminiumnitrid (AlN) aufgrund seiner hervorragenden Wärmeausdehnungsanpassung und moderaten Dielektrizitätskonstanteneigenschaften unter vielen Kandidatenmaterialien hervor und ist zu einer beliebten Wahl für eine neue Generation von Leiterplattenmaterialien geworden. Die Einzigartigkeit des AlN-Substrats erfordert jedoch auch entsprechende Anpassungen und Optimierungen bei der Auswahl der Dickschichtaufschlämmung und dem Produktionsprozess, um die Probleme zu vermeiden, die durch das gleiche Materialsystem und den gleichen Prozess wie beim Al2O3-Substrat verursacht werden.
Durch den Entwurf der Widerstandstestplatte, das Messen und Analysieren der Beziehung zwischen Widerstand und Quadratzahl und die Erforschung der Widerstandsanpassungstechnologie wird in diesem Artikel die Widerstandsherstellungstechnologie auf AlN-Substrat eingehend untersucht. Die Ergebnisse zeigen, dass ein Widerstand mit stabiler Leistung und hoher Präzision auf einem AlN-Substrat hergestellt werden kann, indem das Größenverhältnis des Widerstands angemessen gestaltet und die Prozessparameter präzise gesteuert werden. Diese Forschungsergebnisse liefern nicht nur technische Unterstützung für die Anwendung von AlN-Substraten im Bereich der mikroelektronischen Verpackung, sondern bieten auch eine wirksame Lösung für das Wärmeableitungsproblem elektronischer Komponenten mit hoher Leistungsdichte in der Zukunft. Mit dem kontinuierlichen Fortschritt der Technologie wird die Verbesserung des AlN-Substrats und seines unterstützenden Produktionsprozesses neue Dynamik in die nachhaltige Entwicklung der Mikroelektronikindustrie bringen.