In praktischen Anwendungen wird von Aluminiumnitrid-Substraten neben einer hohen Wärmeleitfähigkeit und hohen elektrischen Isolationseigenschaften in vielen Bereichen auch eine hohe Biegefestigkeit verlangt. Derzeit beträgt die Dreipunktbiegefestigkeit von auf dem Markt befindlichem Aluminiumnitrid üblicherweise 400 bis 500 MPa, was die Förderung und Anwendung von Aluminiumnitrid-Keramiksubstraten, insbesondere im Bereich von IGBT-Leistungsgeräten mit hohen Zuverlässigkeitsanforderungen, erheblich einschränkt. Aufgrund des komplexen Produktionsprozesses und der hohen Produktionskosten von AlN-Materialien sind die meisten inländischen AlN-Materialien immer noch nicht in der Lage, die Anwendungsanforderungen hoher Wärmeleitfähigkeit und hoher Festigkeit zu erfüllen.
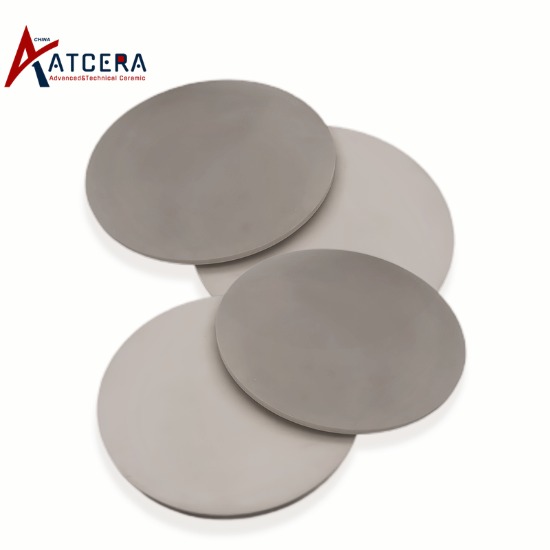
Bei der Herstellung von Aluminiumnitrid-Keramiksubstraten führt die Auswahl der Sintermethoden und Sinterzusätze häufig zu doppelten Ergebnissen bei halbem Aufwand, und die Einführung von Sinterzusätzen ist derzeit eine gängige Methode zum Sintern von Aluminiumnitrid-Keramiken. Einerseits fördern die Bildung einer eutektischen Phase bei niedriger Temperatur und die Verwirklichung des Sinterns in flüssiger Phase den kompakten Körper. Andererseits wird die Sauerstoffverunreinigung im Aluminiumnitrid entfernt, das Gitter verbessert und die Wärmeleitfähigkeit erhöht. Derzeit umfassen die beim Sintern von AlN-Keramiken verwendeten Sinteradditive hauptsächlich Y2O3, CaO, Yb2O3, Sm2O3, Li2O3, B2O3, CaF2, YF3, CaC2 usw. oder deren Mischungen.
Wenn im gesinterten Aluminiumnitrid-Keramikformelsystem Y2O3 mehr als 3,5 Gew.-% beträgt, steigt der Gehalt an Y-Al-O deutlich an und es kommt zur Aggregation im Sinterprozess. Aufgrund der geringen Wärmeleitfähigkeit von Y3Al5O12 (ca. 9 W/(m·K)) wird die Wärmeleitfähigkeit von Aluminiumnitrid-Keramikprodukten nach dem Sintern stark beeinträchtigt. Wenn der Gehalt an CaF2 und Li2O aufgrund der Verflüchtigung von Fluorid und Li-haltigen Verbindungen höher als 1,33 Gew.-% ist, erhöht sich die Porosität des gesinterten Aluminiumnitrid-Keramikkörpers während des Sinterprozesses und die Dichte der Keramik verringert sich Dies führt zu einem starken Rückgang der Biegefestigkeit von Aluminiumnitrid-Keramikprodukten nach dem Sintern. Wenn jeder Zusatzstoff unter dem Mindestwert liegt, kann der Effekt der Verbesserung der mechanischen Eigenschaften nicht erzielt werden oder ist der Effekt sehr gering.
Zusammenfassend lässt sich sagen, dass Aluminiumnitrid-Keramiksubstrate in praktischen Anwendungen den umfassenden Anforderungen einer hohen Wärmeleitfähigkeit, hohen elektrischen Isolationseigenschaften und einer hohen Biegefestigkeit ausgesetzt sind. Die Biegefestigkeit der auf dem Markt befindlichen Produkte ist jedoch im Allgemeinen gering, was ihre breite Anwendung in der Branche einschränkt Bereich hoher Zuverlässigkeit wie IGBT-Leistungsgeräte. Gleichzeitig ist es für das heimische AlN-Material aufgrund des komplexen Produktionsprozesses und der hohen Produktionskosten schwierig, die Anwendungsanforderungen an hohe Wärmeleitfähigkeit und hohe Festigkeit zu erfüllen. Daher ist es bei der Herstellung von Aluminiumnitrid-Keramiksubstraten sehr wichtig, das geeignete Sinterverfahren und die Sinterzusätze auszuwählen, nicht nur um eine eutektische Phase bei niedriger Temperatur zu bilden, um den kompakten Körper zu fördern, sondern auch um Sauerstoffverunreinigungen zu entfernen, um die thermische Leistung zu verbessern Leitfähigkeit. Allerdings müssen Auswahl und Dosierung der Sinteradditive streng kontrolliert werden, um negative Auswirkungen auf die Wärmeleitfähigkeit und Biegefestigkeit zu vermeiden. Um die Leistung von Aluminiumnitrid-Keramiksubstraten zu verbessern, ist es in Zukunft noch notwendig, den Sinterprozess und das Formulierungssystem weiter zu optimieren, um den Anforderungen höherer Anwendungsbereiche gerecht zu werden.