Obwohl die Verarbeitung von Siliziumkarbid-Substrat schwierig ist, soll die Verwendung von einkristallinem Siliziumkarbid in elektronischen Bauteilen zur künftigen Entwicklungsrichtung werden, so dass Siliziumkarbid-Geräte in großem Maßstab eingesetzt und gefördert werden. Es muss ein Weg gefunden werden, das Problem der schwierigen Siliziumkarbidverarbeitung zu lösen.
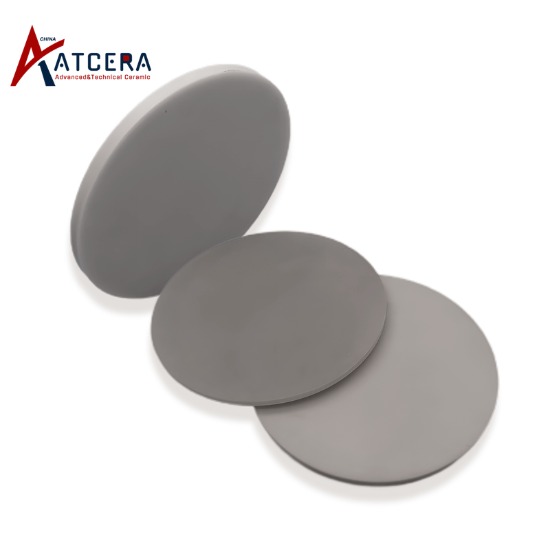
Die SiC-Materialverarbeitungstechnologie umfasst derzeit hauptsächlich die folgenden Prozesse: gerichtetes Schneiden, Span-Grobschleifen, Feinschleifen, mechanisches Polieren und chemisch-mechanisches Polieren (Feinpolieren). Unter diesen ist das chemisch-mechanische Polieren der Endprozess, und die Auswahl der Prozessmethode, die Anordnung der Prozessroute und die Optimierung der Prozessparameter wirken sich direkt auf die Poliereffizienz und die Verarbeitungskosten aus.
Aufgrund der hohen Härte und chemischen Stabilität von SiC-Materialien ist der Materialabtrag beim herkömmlichen CMP-Polierverfahren jedoch gering. Daher begann die Industrie mit der Untersuchung der zusätzlichen Effizienztechnologie zur Unterstützung der Abflachungs-Ultrapräzisionsbearbeitungstechnologie, einschließlich plasmaunterstützter, katalysatorunterstützter, ultravioletter und elektrischer Feldunterstützung, wie folgt:
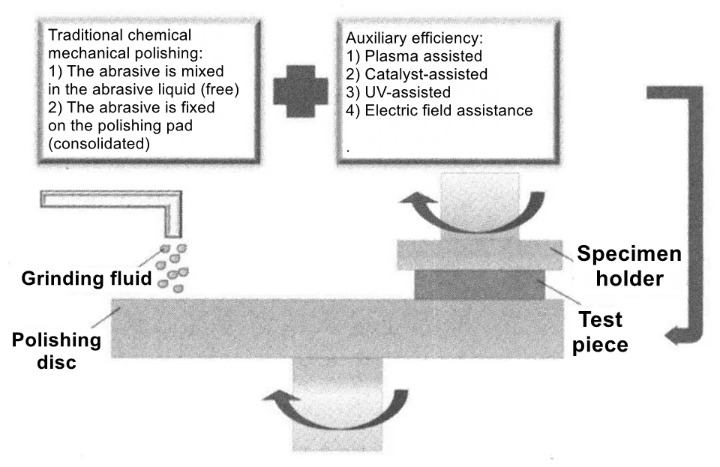
01 Plasmaunterstützte Technologie
YAMAMURA Kazuy et al. schlug zunächst den Prozess des plasmaunterstützten Polierens (PAP) vor, bei dem es sich um ein zusätzliches chemisch-mechanisches Polieren handelt, das Oberflächenmaterialien durch Plasma zu einer weicheren Oxidschicht oxidiert und gleichzeitig Materialien durch abrasive Reibung und Verschleiß entfernt.
Das Grundprinzip besteht darin, durch das Reaktionsgas des HF-Generators (wie Wasserdampf, O usw.) ein Plasma zu erzeugen, das freie Gruppen (wie freie OH-Gruppen, freie O-Radikale) mit einer starken Oxidationskapazität der freien Gruppen enthält Oxidationsmodifikation der Oberfläche des SiC-Materials. Es entsteht eine weiche Oxidschicht, die anschließend durch Polieren mit weichen Schleifmitteln (wie CeO2, Al2O3 usw.) entfernt wird, sodass die Oberfläche des SiC-Materials eine glatte Oberfläche auf atomarer Ebene erreicht. Aufgrund der hohen Preise für PAP-Prozesstestgeräte und Verarbeitungskosten ist jedoch auch die Förderung von SiC-Chips für die PAP-Prozessverarbeitung begrenzt.
02 Katalysatorunterstützter Prozess
Um im industriellen Bereich die hocheffiziente Ultrapräzisionsbearbeitungstechnologie von SiC-Kristallmaterialien zu erforschen, verwenden Forscher Reagenzien für das katalytisch unterstützte chemisch-mechanische Polieren. Der grundlegende Mechanismus der Materialentfernung besteht darin, dass sich unter der Katalyse von Reagenzien eine weiche Oxidschicht auf der SiC-Oberfläche bildet und die Oxidschicht durch die mechanische Entfernung von Schleifmitteln entfernt wird. Für eine hochwertige Oberfläche. In der Literatur wurden Fe3O4-Katalysator und H2O2-Oxidationsmittel verwendet, um die Verbesserung der chemisch-mechanischen Poliertechnologie mit Diamant W0,5 als Schleifmittel zu unterstützen. Nach der Optimierung wurde die Oberflächenrauheit Ra = 2,0 ~ 2,5 nm bei einer Polierrate von 12,0 mg/h erhalten.
03 UV-unterstützte Technologie
Um die Verarbeitungstechnologie zur Glättung der SiC-Oberfläche zu verbessern. Einige Forscher haben ultraviolette Strahlung eingesetzt, um die Katalyse bei chemisch-mechanischen Polierprozessen zu unterstützen. Die photokatalytische UV-Reaktion ist eine der starken Oxidationsreaktionen. Sein Grundprinzip besteht darin, durch photokatalytische Reaktion zwischen Photokatalysator und Elektronenfänger unter Einwirkung von UV-Licht aktive freie Radikale (·OH) zu erzeugen.
Aufgrund der starken Oxidation freier OH-Gruppen. Die Oxidationsreaktion findet auf der SiC-Oberflächenschicht statt und erzeugt eine weichere SiO2-Oxidschicht (MOE-Härte beträgt 7), und die erweichte SiO2-Oxidschicht lässt sich durch abrasives Polieren leichter entfernen; Andererseits ist die Bindungsstärke zwischen der Oxidschicht und der Oberfläche des Wafers geringer als die innere Bindungsstärke des SiC-Wafers, was die Schnittkraft des Schleifmittels beim Polierprozess verringert und die auf dem Wafer verbleibende Kratzertiefe verringert Oberfläche des Wafers und verbessert die Qualität der Oberflächenbearbeitung.
04 Elektrofeldgestützte Technologie
Um die Abtragsrate von SiC-Materialien zu verbessern, haben einige Forscher die Technologie des elektrochemischen mechanischen Polierens (ECMP) vorgeschlagen. Das Grundprinzip ist: Durch Anlegen eines elektrischen Gleichstromfeldes an die Polierflüssigkeit bei der herkömmlichen chemisch-mechanischen Polierbehandlung wird durch elektrochemische Oxidation die Oxidationsschicht auf der SiC-Polieroberfläche gebildet und die Härte der Oxidschicht deutlich verringert. Mit Schleifmittel wird die aufgeweichte Oxidschicht entfernt, um eine effiziente Ultrapräzisionsbearbeitung zu erreichen. Es ist jedoch zu beachten, dass bei schwachem Anodenstrom die Qualität der Bearbeitungsoberfläche besser ist, sich die Materialabtragsrate jedoch nicht wesentlich ändert; Bei starkem Anodenstrom erhöht sich die Materialabtragsleistung deutlich. Ein zu starker Anodenstrom führt jedoch zu einer geringeren Oberflächengenauigkeit und Porosität.
Kurz gesagt ist das chemisch-mechanische Polieren nach wie vor die Methode mit dem größten Potenzial zur Glättung von Ultrapräzisionsbearbeitungsmethoden für SiC-Materialien. Um jedoch qualitativ hochwertige SiC-Wafer effizienter zu erhalten, sind die oben genannten Hilfsprozesse potenzielle Optionen. Aufgrund des Mangels an relevanten Studien sind die Auswirkungen auf SiC-Materialien jedoch noch nicht vorhersehbar. Wenn wir daher den Einfluss verwandter Hilfsprozesse auf die chemisch-mechanische Poliertechnologie eingehend untersuchen und den Verarbeitungsmechanismus der Technologie zur Effizienzsteigerung von chemisch-mechanischen Polierhilfsmitteln durch quantitative und qualitative Forschungsmittel weiter aufdecken können, wird dies für die Realisierung von großer Bedeutung sein die Industrialisierung, Anwendung und Förderung von SiC-Materialien.