Aluminiumnitridkeramik ist ein wichtiges Substratmaterial für die Wärmeableitung. Allerdings besitzt das Aluminiumnitridkeramiksubstrat selbst keine elektrische Leitfähigkeit, sodass die Oberfläche metallisiert werden muss, bevor es als Hochleistungssubstrat zur Wärmeableitung verwendet werden kann.
Die Benetzungsfähigkeit von Metall auf Keramikoberflächen bei hohen Temperaturen bestimmt die Bindungskraft zwischen Metall und Keramik, und eine gute Bindungskraft ist eine wichtige Garantie für die Stabilität der Verpackungsleistung. Daher ist die Realisierung der Metallisierung von Keramiksubstraten ein wichtiger Teil der praktischen Anwendung von Aluminiumnitridkeramiken.
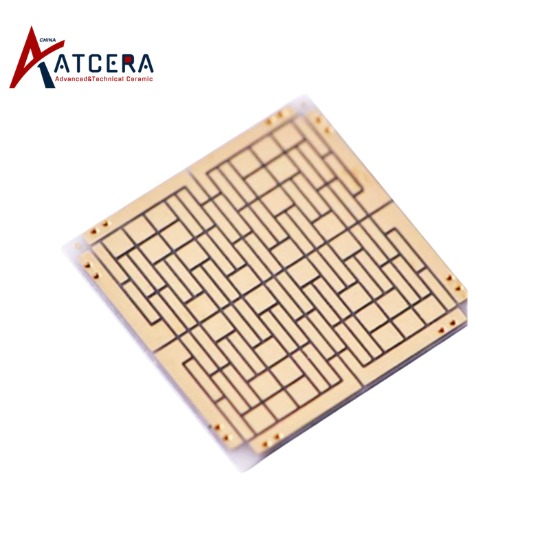
Mechanische Verbindung und Verbindung
Die mechanische Verbindungsmethode zeichnet sich durch eine vernünftige Konstruktion und die Verwendung mechanischer Spannungen aus, um die Verbindung zwischen Aluminiumnitridsubstrat und Metall herzustellen, beispielsweise durch Heißhülsenverbindung und Bolzenverbindung. Die mechanische Verbindungsmethode zeichnet sich durch einen einfachen Prozess und eine gute Durchführbarkeit aus, die Spannung an der Verbindung ist jedoch groß und sie ist nicht für Hochtemperaturumgebungen geeignet und der Anwendungsbereich ist begrenzt.
Beim Bonden wird das organische Bindemittel als Verbindungsmedium verwendet. Durch den entsprechenden Bondprozess werden die Eigenschaften des Aluminiumnitridsubstrats und der Metallmaterialien zu einer mechanischen Gesamtverbindungsmethode kombiniert. Allerdings ist die Bonding-Methode auch nicht für Umgebungen mit hohen Temperaturen und hoher Festigkeit geeignet und der Einsatzbereich ist gering.
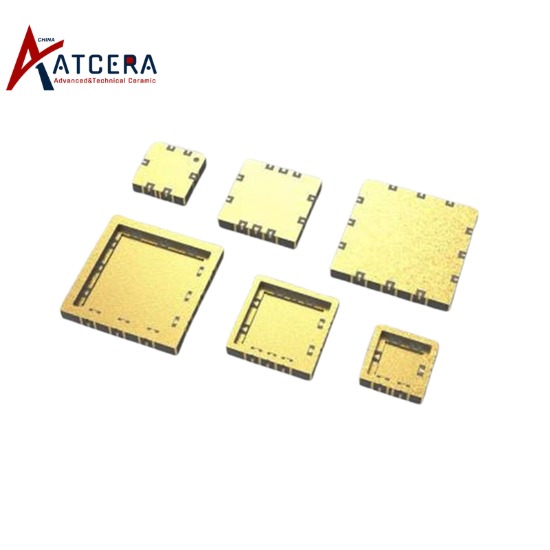
Dickschichtverfahren (TPC)
Bei der Dickschichtmethode handelt es sich um den Prozess, bei dem eine leitfähige Paste im Siebdruckverfahren direkt auf die Oberfläche eines Aluminiumnitrid-Keramiksubstrats aufgetragen und anschließend bei hoher Temperatur getrocknet und gesintert wird, damit die Metallbeschichtung an der Oberfläche des Keramiksubstrats haftet.
Leitfähige Paste besteht im Allgemeinen aus leitfähigem Metallpulver, Glasbindemittel und organischem Träger. Das leitfähige Metallpulver bestimmt die elektrischen und mechanischen Eigenschaften der Paste nach der Filmbildung. Die üblicherweise verwendeten Metallpulver sind Silber, Kupfer, Nickel und Aluminium usw., wobei Silber und Kupfer einen geringen Widerstand und niedrige Kosten aufweisen und für die industrielle Produktion besser geeignet sind.
Daher ist das Verfahren zuverlässig und bietet die Vorteile einer hohen Produktionseffizienz, niedriger Kosten und eines flexiblen Designs. Sein Nachteil besteht darin, dass es durch die Präzision des Siebdruckverfahrens begrenzt ist, die Haftung nicht leicht zu kontrollieren ist und das gesinterte Substrat keine hochpräzisen Linien erzeugen kann, sodass es nur auf Verpackungsmaterialien für elektronische Geräte mit geringen Anforderungen an die Liniengenauigkeit angewendet werden kann.
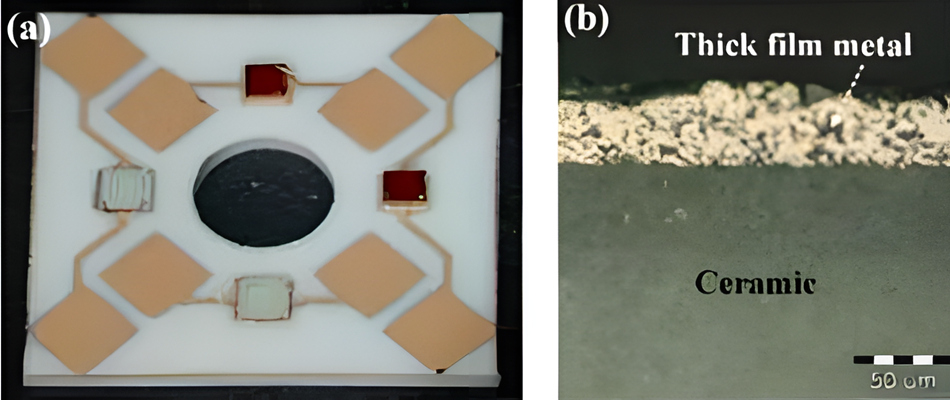
Aktivmetalllöten (AMB)
Bei der aktiven Metalllötmethode werden Ti, Zr, Al, Nb, V und andere Übergangselemente mit relativ aktiven chemischen Eigenschaften direkt in das übliche Lötmetall eingearbeitet. Diese aktiven Elemente reagieren chemisch direkt mit der Oberfläche von Aluminiumnitridkeramik und bilden eine Übergangsschicht. Das Hauptprodukt der Übergangsschicht sind einige Metallbindungsverbindungen und haben die gleiche Struktur wie das Metall, sodass sie vom geschmolzenen Füllmetall benetzt werden kann, um eine metallurgische Verbindung zu bilden.
Aluminiumnitrid-Keramiksubstrate sind wichtige Wärmeableitungsgeräte und werden häufig bei hohen Temperaturen verwendet. Daher werden mehr Hochtemperaturverbindungen benötigt. Das hauptsächlich aus CuTi und NiTi bestehende Hochtemperatur-Aktivlot kann im Bereich von 1200 bis 1800 °C verwendet werden. Das am häufigsten verwendete Hochtemperatur-Aktivlot ist das ternäre System oder Mehrkomponentensystem, das durch Au-, Co- und PD-basiertes Lot repräsentiert wird. Der Schmelzpunkt von Au, Co und Pd beträgt 1064 °C, 1492 °C bzw. 1554 °C, was zur Erhöhung des Schmelzpunkts des Lots beiträgt.
Da die aktiven Elemente im Lötmetall chemisch aktiv sind, muss das Aktivlöten, um chemische Reaktionen mit Sauerstoff bei hohen Temperaturen zu vermeiden, unter dem Schutz einer starken Vakuumumgebung oder einer inerten Atmosphäre durchgeführt werden, was mit hohen technischen Kosten verbunden ist und es nicht für Anwendungen im großen Maßstab geeignet ist.
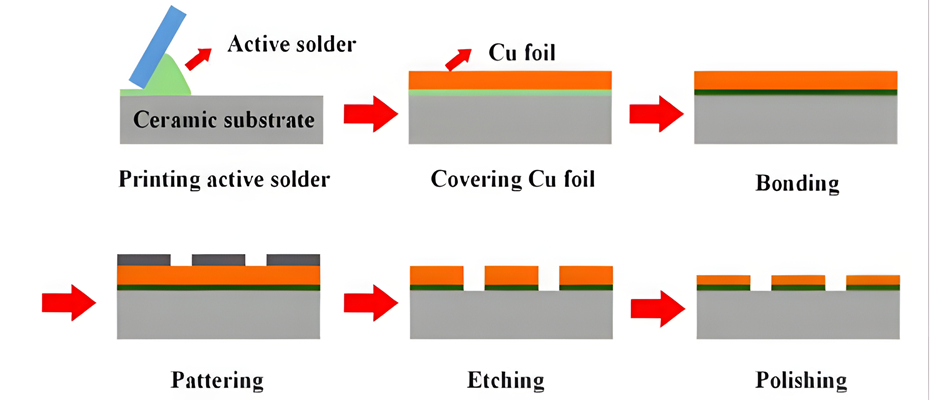