Siliziumkarbid-Substrat hat als neue Generation von Halbleiterprodukten aufgrund seiner hervorragenden physikalischen und chemischen Eigenschaften ein großes Anwendungspotenzial im Bereich leistungselektronischer Geräte gezeigt. Allerdings ist die hohe Effizienz und das verlustarme Schneiden von SiC-Ingots eine der Schlüsseltechnologien, die die Massenproduktion einschränken. Derzeit sind Mörteldrahtschneiden und Diamantdrahtschneiden die beiden Haupttechnologien beim Schneiden von SiC-Ingots, und sie weisen erhebliche Unterschiede in der Art der Schleifmitteleinbringung, der Verarbeitungseffizienz, dem Materialverlust und der Umweltbelastung auf. Ziel dieses Artikels ist es, die Eigenschaften dieser beiden Schneidtechnologien zu vergleichen und zu analysieren und die Optimierungsrichtung des SiC-Schneidprozesses zu diskutieren.
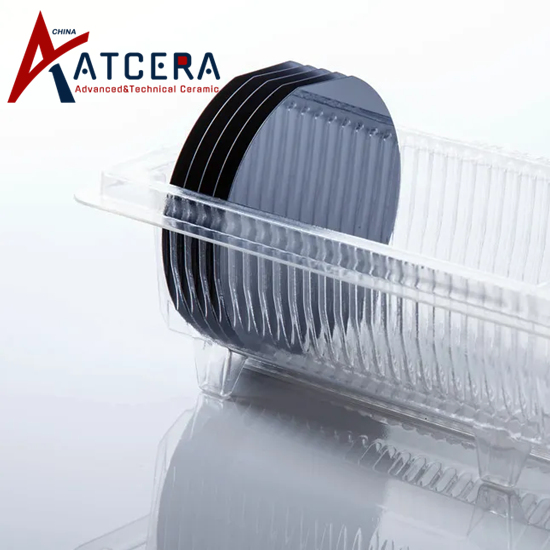
1. Schleifmittelimportmodus und Verarbeitungseffizienz
· Mörteldrahtschneiden: Bei Verwendung von freiem Schleifmittel ist die Verarbeitungsgeschwindigkeit relativ langsam.
· Diamantdrahtschneiden: Durch Galvanisieren, Harzbinden und andere Methoden zur Fixierung der Schleifpartikel wird die Schnittgeschwindigkeit um mehr als das Fünffache erhöht und die Produktionseffizienz erheblich verbessert.
2. Materialverlust und Filmausstoßrate
· Mörteldrahtschneiden: geringe Ausstoßleistung, großer Materialverlust.
· Diamantdrahtschneiden: Die Ausbringungsleistung wird um 15 % bis 20 % erhöht, der Materialverlust deutlich reduziert und der wirtschaftliche Nutzen verbessert.
3. Vorteile für den Umweltschutz
· Diamantdrahtschneiden: Weniger Abfall und Abwasserproduktion, umweltfreundlicher.
4. Technische Herausforderungen und Bewältigungsstrategien
· Diamantdrahtschneiden: Es gibt Herausforderungen bei der Kristallkontrolle und der Schnittverlustkontrolle.
· Bewältigungsstrategie: Die aktuelle Industrie übernimmt die Strategie des Mörteldrahtschneidens als Haupt- und Diamantdrahtschneiden als Hilfsstrategie, das Nutzungsverhältnis beträgt etwa 5:1. In Zukunft ist es notwendig, die Diamantdrahtschneidetechnologie weiter zu optimieren, um ihre Wettbewerbsfähigkeit beim SiC-Schneiden zu verbessern.
5. Verarbeitungsverlustanalyse von SiC-Materialien
· Mörteldraht-Schnittverlust:
· Kerbverlust: bis zu 150–200 Mikrometer.
· Polierverlust: Oberflächenschäden müssen durch Grobschleifen, Feinschleifen und CMP-Prozesse repariert werden.
· Rückverdünnungsverlust: Die anfängliche Dickeneinstellung ist hoch, die Rückverdünnung ist erforderlich, um den Widerstand zu reduzieren.
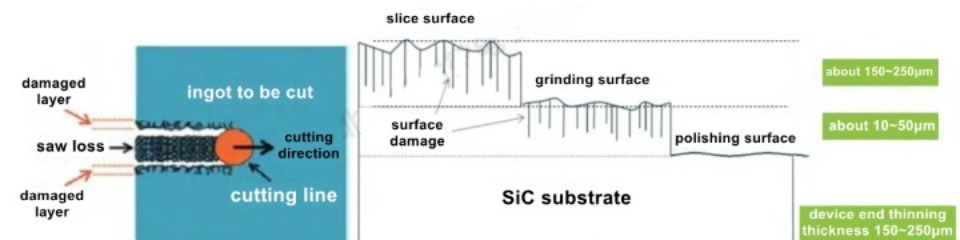
SiC-Schnittverlust und -schäden
Zusammenfassend lässt sich sagen, dass die Diamantdrahtschneidetechnologie beim Schneiden von SiC-Ingots erhebliche Vorteile bei der Verarbeitungsgeschwindigkeit, geringeren Materialverlusten und Umweltschutzvorteilen aufweist, ihre Kristallkontrolle und Schnittverlustkontrolle müssen jedoch noch weiter optimiert werden. Derzeit ist die komplementäre Einsatzstrategie des Mörteldrahtschneidens und des Diamantdrahtschneidens eine gängige Praxis in der Branche. Mit dem kontinuierlichen Fortschritt der Diamantdrahtschneidetechnologie und der Kostensenkung wird erwartet, dass sie in Zukunft eine führende Stellung im Bereich des SiC-Schneidens einnehmen wird. Gleichzeitig ist es angesichts der Verlustproblematik bei der Verarbeitung von SiC-Materialien erforderlich, effizientere und verlustarme Schneid- und Polierverfahren weiter zu erforschen, um die effiziente und kostengünstige Produktion von SiC-Halbleitermaterialien voranzutreiben und zu fördern breite Anwendung im Bereich leistungselektronischer Geräte.