Mit der rasanten Entwicklung der Leistungselektroniktechnologie, insbesondere der breiten Anwendung von Leistungshalbleiterbauelementen wie Hochspannungs-, Hochstrom- und Hochfrequenz-IGBT-Modulen, werden strengere Anforderungen an mit Kupfer beschichtete Keramiksubstrate gestellt. Als eine Art Keramikmaterial mit hoher Wärmeleitfähigkeit, niedriger Dielektrizitätskonstante und guten mechanischen Eigenschaften ist Aluminiumnitrid (AlN) eine ideale Wahl für die Herstellung von kupferbeschichteten Hochleistungskeramiksubstraten. Die Oberflächeneigenschaften des Aluminiumnitrid-Substrats erschweren jedoch die Benetzung und Ausbreitung von Kupfer und Kupferoxiden, was seine direkte Anwendung auf DBC-Prozesse (Direct Bonded Copper) einschränkt. Daher ist die Erforschung des effizienten Herstellungsprozesses von kupferplattierten Aluminiumnitrid-Keramikplatten und die Optimierung ihrer Leistung zum Schwerpunkt der aktuellen Forschung geworden.
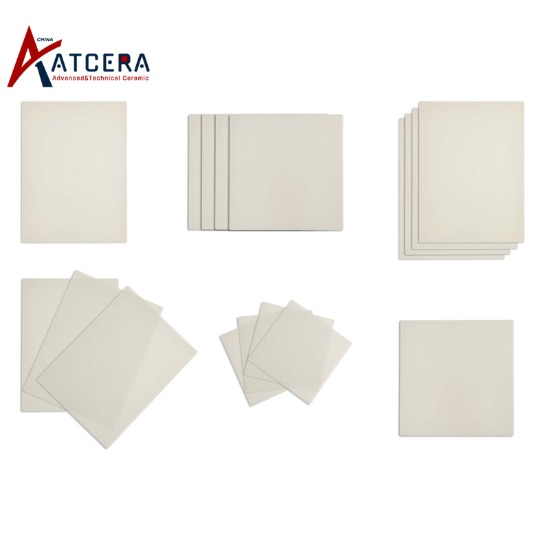
Herausforderungen und Lösungen für den Herstellungsprozess von Aluminiumnitrid-DBC: Die Oberflächeneigenschaften von Aluminiumnitrid erschweren die direkte Verbindung mit Kupfer. Die Benetzbarkeit von Kupfer und Kupferoxiden auf der Oberfläche von Aluminiumnitrid kann durch die Bildung einer dichten und gleichmäßigen Aluminiumoxid-Verbundschicht auf der Oberfläche von Aluminiumnitrid erheblich verbessert werden. Das DBC-Verfahren nutzt die eutektische Verbindung von Kupfer und Aluminiumoxid und realisiert die feste Verbindung von Keramik und Kupferfolie durch Kettenofensintern.
Einführung und Vorteile des AMB-Prozesses: Als Verbesserung des DBC-Prozesses nutzt der AMB-Prozess (Aktivmetalllöten) das aktive Element im Füllmetall (z. B. Ti), um mit der Keramik zu reagieren und eine Reaktionsschicht zu erzeugen (z. B. TiN), das vom flüssigen Zusatzmetall benetzt werden kann und so die Bindungskraft der Keramik- und Kupferfolie erhöht. Der AMB-Prozess erfordert Vakuumsintern, um eine Oxidation des aktiven Metalls zu verhindern, und obwohl die Prozesskomplexität zunimmt, ist die Bindungskraft stärker und die Zuverlässigkeit höher.
Vergleich des DBC- und des AMB-Prozesses: Der DBC-Prozess verwendet ein einstufiges Kupferätzen, während der AMB-Prozess aus einem einstufigen Kupferätzen und einem einstufigen TiN-Ätzen besteht, wobei der letztere Prozess schwieriger ist. Allerdings ist die Bindungskraft von AMB-AlN der von DBC-AlN überlegen und weist eine höhere Zuverlässigkeit und Leistung auf.
Richtung der Leistungsoptimierung von kupferbeschichteten Aluminiumnitrid-Keramikplatten: Mit der Entwicklung von Leistungshalbleiterbauelementen verbessern sich die Leistungsanforderungen von kupferbeschichteten Keramiksubstraten ständig. Die Verbesserung der Festigkeit von Aluminiumnitridkeramiken und die weitere Optimierung des Herstellungsprozesses zur Erzielung höherer Zuverlässigkeit, Temperaturbeständigkeit und Stromtragfähigkeit sind wichtige Richtungen der weiteren Forschung.
Zusammenfassend lässt sich sagen, dass der Herstellungsprozess von kupferplattierten Aluminiumnitrid-Keramikplatten durch die Einführung der aktiven Metalllöt- und Vakuumsintertechnologie eine Weiterentwicklung von DBC zu AMB durchlaufen hat, wodurch das Problem der Benetzbarkeit der Aluminiumnitridoberfläche effektiv gelöst und die Bindungskraft erheblich verbessert wurde und allgemeine Zuverlässigkeit von Keramik und Kupferfolie. Mit dem kontinuierlichen Fortschritt der Leistungshalbleitertechnologie steigen jedoch auch die Leistungsanforderungen an kupferbeschichtete Keramiksubstrate. Daher sollte sich die zukünftige Forschung auf die weitere Optimierung des Herstellungsprozesses und die Verbesserung der Festigkeit von Aluminiumnitridkeramiken konzentrieren, um den Verpackungsanforderungen von Hochleistungs-Leistungshalbleiterbauelementen wie Hochspannungs-, Hochstrom- und Hochfrequenz-IGBT-Modulen gerecht zu werden und die nachhaltige Entwicklung zu fördern der Leistungselektroniktechnik.