In der sich schnell verändernden Elektronikindustrie von heute sind keramische Substratmaterialien eine wichtige Grundlage für die Unterstützung leistungsstarker elektronischer Geräte. Ihre Leistung und Eigenschaften wirken sich direkt auf die Gesamtleistung und Zuverlässigkeit elektronischer Produkte aus. Von den frühen Aluminiumoxidkeramiken bis hin zu den späteren Aluminiumnitriden, Siliziumnitriden und anderen neuen Materialien war die Entwicklung keramischer Substratmaterialien Zeuge des kontinuierlichen Fortschritts und der Innovation von Wissenschaft und Technologie. In diesem Artikel erfahren Sie mehr über die einzigartigen Vorteile und Anwendungsaussichten dieser keramischen Substratmaterialien, insbesondere darüber, wie sich Aluminiumnitrid- und Siliziumnitrid-Keramiken durch ihre hervorragende Leistung bei der Lösung der Wärmeableitung von Hochleistungsgeräten und Umgebungen mit hoher Wärmeableitung auszeichnen und werden zu einem unverzichtbaren wichtigen Material in der modernen Elektronikindustrie.
Aluminiumoxidsubstrat, als Pionier des Keramiksubstrats, wurde seit 1929 von Siemens in Deutschland erfolgreich entwickelt und ging 1933 in die industrielle Produktion ein. Mit seinem niedrigen Preis, seiner hervorragenden Stabilität, seiner guten Isolierung und seinen mechanischen Eigenschaften hat es in einer Vielzahl von Bereichen seit langem eine beherrschende Stellung eingenommen Anwendungen. Allerdings schränken seine relativ niedrige Wärmeleitfähigkeit und sein Wärmeausdehnungskoeffizient, die nicht denen von Si entsprechen, seine Weiterentwicklung in Hochleistungselektronikprodukten ein und werden hauptsächlich im Bereich der Niederspannungs- und Schaltungsverpackung mit geringer Integration eingesetzt.
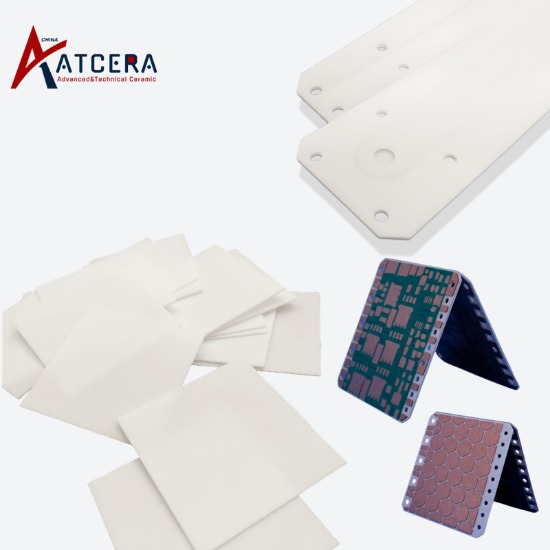
Obwohl sich BeO-Substrate durch ihre hohe Wärmeleitfähigkeit auszeichneten, wurde das Toxizitätsproblem später zu einem unüberwindbaren Hindernis, das nicht nur in Japan verboten, sondern auch in Europa stark eingeschränkt wurde, was seine breite Anwendung erheblich behinderte .
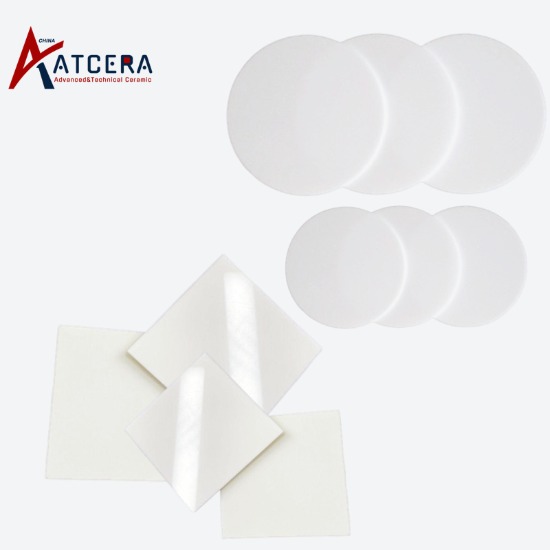
Obwohl der SiC-Einkristall im Gegensatz dazu eine erstaunliche Wärmeleitfähigkeit aufweist, nimmt die Wärmeleitfähigkeit polykristalliner SiC-Keramiken aufgrund der unterschiedlichen Kornorientierung, gepaart mit einer schlechten Isolationsleistung und einem hohen dielektrischen Verlust, erheblich ab, was die Forschung auf diesem Gebiet vorantreibt Leiterplattenmaterialien langsam.
Vor diesem Hintergrund entstehen nach und nach Aluminiumnitrid- und Siliziumnitridkeramiken mit ihren einzigartigen Leistungsvorteilen. Aluminiumnitrid-Substrat mit seiner hervorragenden hohen Wärmeleitfähigkeit (theoretischer Wert bis zu 320 W/(m·K), kommerzielle Produktwärmeleitfähigkeit liegt ebenfalls zwischen 180 W/(m·K) und 260 W/(m·K) ) ist zu einem Schlüsselmaterial zur Lösung des Wärmeableitungsproblems von Hochleistungsgeräten geworden und hat sich seit den 1980er Jahren unter der Förderung entwickelter Länder, insbesondere Japans, schnell zu einer neuen Generation fortschrittlicher keramischer Verpackungsmaterialien entwickelt. Seine hohe mechanische Festigkeit und chemische Stabilität gewährleisten einen stabilen Betrieb in rauen Umgebungen.
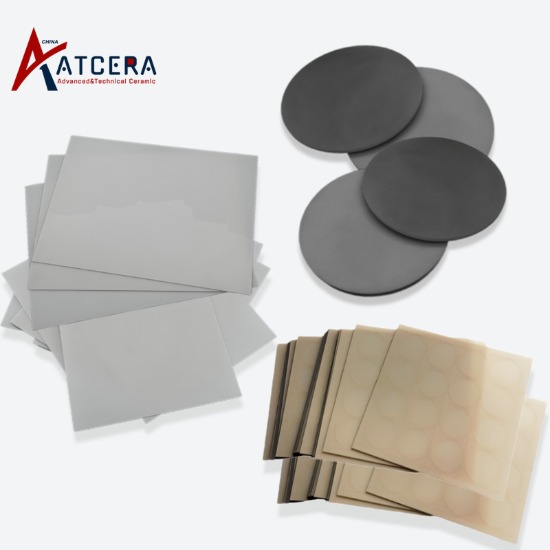
Siliziumnitrid-SubstrateNach dem frühen Stadium der unterschätzten Wärmeleitfähigkeit wurde die Wärmeleitfähigkeit durch wissenschaftliche Forschung und Prozessoptimierung deutlich verbessert und durchbrach 177 W/(m·K), während gleichzeitig ein sehr niedriger Wärmeausdehnungskoeffizient (3,2×10−) beibehalten wurde 6/â) und wird zu einem der hervorragendsten Keramiksubstratmaterialien mit umfassender Leistung. Seine ausgezeichnete Biegefestigkeit und Verschleißfestigkeit zeigen eine außergewöhnliche Wettbewerbsfähigkeit in Umgebungen mit hoher Wärmeableitung.
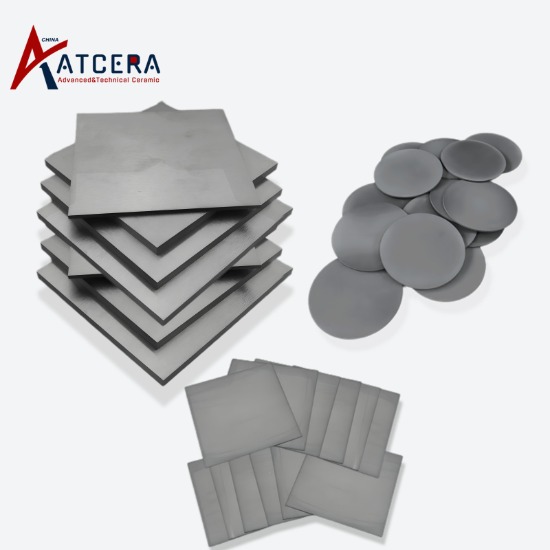
Zusammenfassend lässt sich sagen, dass Aluminiumnitridkeramik aufgrund ihrer hohen Wärmeleitfähigkeit und ihres Wärmeausdehnungskoeffizienten, die zu Halbleitermaterialien passen, die beste Wahl für die Wärmeableitung von Hochleistungsgeräten ist. Siliziumnitridkeramik ist mit ihren umfassenden Leistungsvorteilen führend in anspruchsvollen thermischen Umgebungen. Zusammen führen beide dazu, dass die Keramiksubstratmaterialien eine höhere Leistung und ein breiteres Anwendungsspektrum erreichen.